在制造诸如汽车车身或飞机机身等大型整体复合材料部件时,为了确保精准度并尽可能降低成本,通常采用的是繁复且大型的模具技术。然而,我国科研工作者已经发现通过运用多样化的连接技术,如紧固件、粘合剂粘接以及混合方式等,能有效地将一系列规模相对较小的零部件组合整合为大规模的整体部件,成为制造大型整体部件的理想替代方案。
在众多可供选择的连接技术中,塑料螺栓因其方便的安装、易于检查及有限的表面处理需求而成为制造商钟爱的首选。此外,尽管此类连接方式可能存在一些不足之处,例如基材上的孔洞可能导致应力集中,并且会额外增加整体结构的重量,同时,塑料螺栓的价格较为昂贵,可能占据复合材料飞机结构总成本的19%至42%,但这些问题都可以通过合理设计和优化来解决。 
资料图
焊接作为另一种可行的选择,尤其适用于热塑性塑料的加工。例如,波音公司曾进行过一项研究,结果显示与使用螺纹紧固件相比,采用焊接技术对复合材料机翼结构进行装配所需要的人工劳动量减少了高达61%。
在此基础上,我们还可以进一步具体探讨电阻焊的优点。此方法是通过将导电材料的丝束或编织结构放置于接头处,然后通电,利用电阻产生的热量熔融周围的聚合物以形成稳定可靠的焊接缝。这种技术的另一大亮点在于能够高效焊接大型和复杂的接头,但需要注意的是,导电材料的使用将会进一步增加总生产成本。此外,还有一种被称为感应焊接的方法,其原理是在焊缝线上移动感应线圈,通过感应线圈在导电的碳纤维复合材料层压板中的感应出涡流,进而产生热量熔融聚合物,完成焊接过程。
超声波焊接的优点和局限性
超声波焊接是焊接热塑性塑料的第三个方法。其优点主要有:·超声波焊接是最快的连接方法,是自动化的理想选择。
·因为热量是在焊接面而不是在顶部产生的,表面损伤达到最小化。·该工艺仅限于重叠接头和剪切接头,最大零件厚度被限制在3毫米左右(超声波振动可能难以穿透较厚的部件)。
·具有高刚度、高硬度和高阻尼的材料会阻碍将振动转化为热能的能力。·超声波焊接的工作原理是将机械振动传递到接头处,因此该过程可能会产生尖锐的噪音。此外,由于振动周期性负载,增加了零件疲劳失效的风险。影响聚合物可焊性的特性是其分子结构、熔体温度、流动性、刚度和化学成分。熔体温度与焊接所需的能量成正比。熔体温度越高,焊接所需的超声波能量就越多。刚度影响能量传输,坚硬的材料比柔软的材料更能传递振动。熔体温度和流动性等特性在焊接不同的聚合物时发挥更大的作用。如果一种材料的熔化温度比另一种低,它就会提前熔化,造成不良的接头。为了获得最佳效果,两种材料之间的熔融温度差异不应超过22℃,且两种材料在化学性质上应该是相容的。水分含量也会影响焊接质量。在100摄氏度时,塑料吸收的水分会蒸发,在接头面形成多孔状态,从而降低焊接强度。脱模剂、增塑剂和耐冲击改性剂也会降低树脂传递振动的能力。需要提示的是,填充剂和扩展剂通过赋予树脂更高的硬度,提高了传输超声波能量的能力。然而,控制填充物的比例是很重要的。使用高达20%的填充物在传递振动方面有积极的效果,但添加更多的填充物可能导致衔接处树脂量不足,从而降低焊接质量。接头设计
超声波焊接主要应用于两种类型的接头:导能筋接头(Energy Director Joints)和剪切接头(Shear Joints)。导能筋(ED)是铸在其中一个部件上的突起。对接接头(Butt Joint)和搭接接头(lap Joints)也通常使用导能筋。对于剪切接头,振动传递的方向与焊接面平行,由焊接面上的摩擦剪切力而产生热量。当需要强大的结构性能或密封性时,可使用剪切接头,非常适用于焊接半结晶树脂。
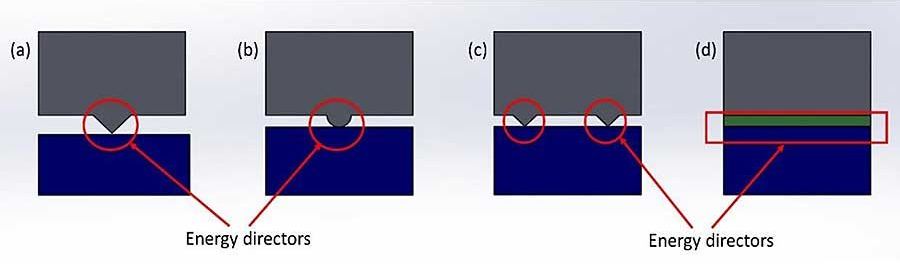
导能筋的类型
导能筋是超声波焊接中一个重要的物理结构。它有助于通过将能量集中在接头界面,来增强粘弹性加热。导能筋的大小和形状会影响焊接质量。它可以是半圆形的,三角形,或扁平的。它们的方向也可以与接头平行或垂直。扁平的导能筋通常足以用于焊接纤维增强的复合材料。导能筋的几何形状对焊接质量也有很大影响。例如,一项研究考察了碳纤维增强的聚醚酰亚胺的超声波焊接。研究人员发现,焊接强度随着导能筋体积的增加而增加,直至某一点。在一定的体积阈值之后,焊接强度下降。特殊情况下,热塑性复合材料也可以在没有导能筋的情况下进行焊接。然而,有总比没有好。一项研究表明,在连接尼龙6复合材料时,导能筋对焊接质量的影响比焊接力或振动时间更重要。另一项研究也发现,在焊接碳纤维增强的PEEK时,有导能筋的接头,搭接剪切焊接强度比没有的高50%。超声波焊接参数
超声波焊接质量同时受几个参数的制约,包括振动幅度,功率,输入能量,焊接时间,焊接过程中的垂直位移,焊接前、中、后的施力,最后是保持时间。
焊接质量主要取决于输入能量。输入能量可以通过公式计算。E = F×f×A×t,其中E是输入能量,F是焊接力,f是频率,A是振幅,t是时间。最佳的焊接强度与总能量输入密切相关。例如,还是对纤维增强尼龙6的研究中发现,200到1000焦耳的总能量输入增加了焊接强度。但超过1000焦耳的能量会导致接头中出现孔隙,从而降低了强度。焊接时间是另一个关键参数。在涉及碳纤维增强PEEK的研究发现,焊接质量随着焊接时间从0.7秒增加到0.8秒而提高。较长的焊接时间(1.1秒或以上)在接头上产生了裂缝和空隙。最终,0.9秒是获得良好焊接质量的最佳时间。热塑性复合材料与其他材料的焊接
许多研究都关注热塑性复合材料与其他材料的焊接问题,如热固性复合材料、铝和钢。由于超声波焊接取决于每个基材的熔化情况,热固性复合材料之间的焊接是不可行的。然而,也可以将热固性复合材料焊接到热塑性薄膜上,如PEEK、聚砜、聚苯硫醚、聚苯乙烯、聚醚酰亚胺和聚乙烯醇。加工温度是影响这种焊接生产效果的主要因素。必须注意防止在焊接过程中热固性复合材料的热降解。焊接时间短是最理想的。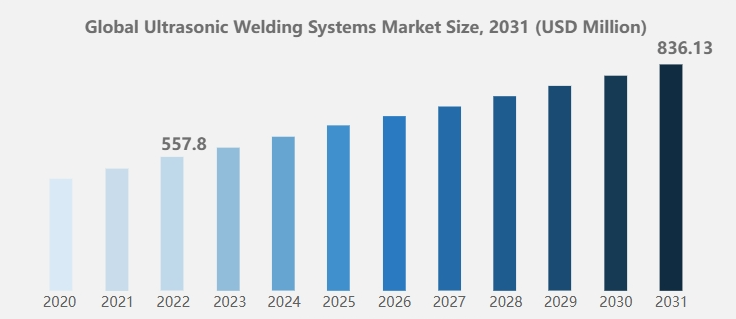
全球超声焊接市场规模2020-2031年(百万美元)
据统计,2022年度全球超声波焊接系统市场规模达到了5.578亿美元,而预计至2031年其市场规模将进一步攀升至8.3613亿美元,在此期间的复合年增长率预计为4.6%。超声波焊接技术的应用领域极为广泛,涉及电气、个人电脑、汽车、航空航天、医学临床以及绑定安装等等多个产业领域内的企业都能从中受益匪浅。然而,我们需要明确的是,两个物品能否通过超声波实现无缝衔接,并非仅仅取决于物体本身的厚度。超声波焊接作为一项广为人知且颇具特色的热塑性塑料焊接技艺,凭借其迅速、轻松的自动化特性而被广大用户所吸纳。焊接所需时间通常仅需短短一秒以内,无需设置通风框架,同时也预期能够达到消除应力及排气的效果。这种独特的焊接方式已被广泛运用于制造微小聚集体,甚至在某些情况下,对于常规焊接手段而言过于脆弱的物体也能得到妥善处理。正是由于其多样化的应用场景与显著优势,才使得超声波焊接系统市场得以稳步发展壮大。在医学临床领域,超声波焊接技术的运用尤为频繁,原因在于其不会对焊缝产生任何毒性物质或降低其品质,同时该设备还可专门用于洁净室环境。这种特殊的交互作用同样可以实现高度自动化,对层状电阻进行精确控制,同时也不会影响部件的生物相容性。借助此种技术,不仅能够提升零部件的质量水平,同时还能有效降低制造成本。例如,血管通道、镇静通道、血液通道、静脉导管、透析管、移液器、心脏测量库、血液或气体通道、面部覆盖物以及静脉尖峰或通道等多种医疗器械均可采用超声波焊接系统进行加工制作。此外,超声焊接在医学临床领域的另一大重要应用便是材料处理。急救诊所的设备、清洁衣物、盖布、透皮贴片以及洁净室材料等皆可用超声波焊接技术进行固定和缝合,从而避免污染物和残留物的产生,大大降低污染发生的风险。预估这些日益增长的需求将会进一步助推超声波焊接系统市场占有率的提升。对于汽车制造业而言,超声波焊接技术常常被广泛应用于诸如仪表板、舱门板、灯具、气管、导向轮、内部装饰以及电动马达部件等大型塑料和电器元件的布局拼接过程中。随着塑料在各式汽车的设计规划以及生产工艺中所占据比重逐渐加大,如何精确高效地组装和连接塑料零部件就成为了一道亟待解决的难题。而超声波焊接技术之所以受到人们青睐,首先就是其工艺持续时间短,易于实现机器人化操作,同时投资成本较低;其次,超声波焊接技术具有出色的适应能力,深受各大航空产业青睐,同时也适用于连接薄板、检测金属以及其他轻质材料。尤其值得一提的是,由于铝材具有极高的导热性能,因此采用传统焊接方法对其进行处理往往较为困难。预计以上诸多因素以及其多元化的应用场景将在未来几年内继续推动超声波焊接系统市场的蓬勃发展。
此文由中国复合材料工业协会搜集整理编译,部分数据来源于网络资料。文章不用于商业目的,仅供行业人士交流,引用请注明出处。