树脂灌注成型工艺(Resin Transfer Molding——RTM)是从湿法铺层和注塑工艺演变而来的一种新的复合材料成型工艺,RTM的技术起源,有资料认为是起源于20世纪40年代的“MARCO”方法。初期开发的技术主要在欧洲,在60年代至70年代,玻璃钢领域将重点放在喷射和片状模塑料成型上,RTM虽然成本较低,但其技术要求较高,特别是对原材料及模具的要求较高,大规模推广有一定的困难,因而发展缓慢。到了20世纪80年代,由于工业发达国家对生产环境要求的各项法规日趋严格,如美国、英国对工作区苯乙烯的限量浓度为100×10-6,北欧和日本限量浓度为50×10-6等,为此,生产厂家不得不放弃传统的手糊和喷射成型工艺,寻找符合环保法规的低苯乙烯挥发量的工艺。同时,随着原材、工艺的发展和成型技术的不断进步,加上RTM工艺自身诸多的优点,如模制件公差小,有很高的表面质量,与SMC比较模塑压力小,生产加工组织方式多种多样,投资少,生产效率较高等特点而受到各国的重视。 1985年前后,以缩短成型周期、提高表面质量平顺性和提高质量稳定性为目标的第二代RTM开始得到应用。第二代RTM的典型特征是使用中温固化体系,纤维使用预成型的方式,生产效率得到大幅度提高,单模生产周期缩短到20~30分钟,真空辅助成型得到了普遍应用。以更高效率为特点的第三代RTM工艺在20世纪90年代中期开始得到应用,聚酯类树脂的成型温度提升到120℃以上,成型效率达到了单模生产5分钟。代表性的产品有法国Sortira公司为福特生产的轿车扰流板,日产量可以达到800件,生产效率完全可以和SMC相比。 RTM工艺一个重要发展方向是大型部件的整体成型。工艺方法以VARTM、Light-RTM、SCRIMP工艺为代表,主要应用于汽车、船艇、风机叶片等大型或者特大型部件的整体成型。进入21世纪以后,RTM工艺在大型结构部件的制造中表现出了明显的优势,在各领域得到了越来越多应用。 国内的RTM工艺的起步于20世纪80年代末期,受当时国际RTM技术高速发展的影响,一些中小型企业基于想改变传统手工操作局面的想法,引进了许多RTM注射设备,一度形成“热点”。但是由于受当时原材料配套系统的不完善和基础工艺理论研究欠缺的影响,未能形成规模化生产,大部分设备都处于闲置状态。20世纪90年代以后,国内一些单位积极研究和推广RTM工艺技术,从原材料、产品设计、模具设计与制造、A级表面技术和基础理论以及工业化生产技术等方面,开展了系统的研究工作。期间比较有代表性的产品在民用领域有富康轿车背门、奥拓轿车尾翼、座椅、电话亭等产品。进入21世纪后,随着三维编织技术的快速发展,RTM在飞机部件和其它军用产品上得到了较多的应用,而随着Light-RTM 和SCRIMP在游艇和风机叶片上的应用,该类型工艺的应用优势越来越多地得到了大家的认可和熟悉。 RTM工艺技术的研究和应用涉及材料学、流体力学、化学、计算机模拟仿真及实时监控技术等诸多交叉学科领域,是当前国际复合材料最活跃的研究领域之一。其主要研究方向包括:低黏度高性能树脂体系的制备及其化学动力学和流变特性;纤维预成型体的制备及渗透特性;成型过程的计算机模拟仿真技术;成型过程的在线监控技术;模具优化设计技术;新型工艺设备的开发;成本分析技术等。 RTM以其优异的工艺性能,已广泛地应用于舰船、军事设施、国防工程、交通运输、航空航天和民用工业等。其主要特点如下:(1)模具制造和材料选择灵活性强,根据不同的生产规模,设备的变化也很灵活,制品产量在1,000-20,000之间,采用RTM成型工艺可获得最佳生产经济效益。(2)能制造具有良好表面质量、高尺寸精度的复杂部件,在大型部件的制造方面优势更为明显。(3)易实现局部增强、夹芯结构;容易灵活调整增强材料的类型、结构设计,以满足从民用到航空航天工业不同性能的要求。(5)RTM成型工艺属一种闭模操作工艺,工作环境清洁,成型过程苯乙烯排放量小,有利于环保。(6)RTM成型工艺对原材料体系要求严格,要求增强材料具有良好的耐树脂流动冲刷和良好的浸润性,要求树脂黏度低,高反应活性,中温固化,固化放热峰值低,浸渍过程中黏度较小,注射完毕后能很快凝胶。(7)低压注射,一般注射压力<30psi,可采用玻璃钢模具(包括环氧模具、玻璃钢表面铸镍模具等),铝模具等,模具设计自由度高,模具成本较低。 与预浸料模压工艺相比,RTM工艺无需制备、运输、储藏冷冻的预浸料,无需繁杂的手工铺层和真空袋压过程,也无需热处理时间,操作简单。技术的开发和扩大应用之所以活跃,主要是因为其工艺过程前期树脂和纤维相对分离,纤维材料的组合自由度非常大,不同类型的纤维以及不同结构形式的编织方法都可以应用,多种类型的树脂也可以根据产品需要来选择。 但是RTM工艺由于在成型阶段树脂和纤维才通过浸渍过程实现赋型,纤维在模腔中的流动、纤维浸渍过程以及树脂的固化过程都对最终产品的性能有很大的影响,因而导致了工艺的复杂性和不可控性增大。表6-1列出了手糊、RTM、SMC/BMC成型方法适用性的比较。
比较 | 手糊 | RTM | SMC/BMC |
生产规模 (件/年) | 小于1000 | 5,000-10,000 | 10,000以上 |
模塑温度 | 室温 | 40-60℃(室温也可以) | 130-150℃ |
成型周期 | 1-4h | 5-30min | 1-15min |
生产效率/8h | 2-3 | 16-90 | 50-400 |
模具类型 | FRP | FRP或金属 | 金属 |
模具费(以开模为1) | 1 | 2-4 | 5-10 |
制品表面效果 | 一面光 | 两面光 | 两面光 |
部件重复性 | 人为因素影响较大 | 较好 | 很好 |
部件尺寸精度 | 人为因素影响较大 | 较好 | 很好 |
树脂、纤维比例 | 人为因素影响较大 | 较好 | 很好 |
填料含量 | 高 | 较低 | 高 |
脱模剂 | 外脱模 | 内外都可 | 内脱模 |
压力 | 接触压力 | 0.1-0.25 MPa | 4-10MPa |
RTM工艺的基本原理如图6-1所示,先在模腔内预先铺放增强材料预成型体、芯材和预埋件,然后在压力或真空作用力下将树脂注入闭合模腔,浸润纤维,固化后脱模,再进行二次加工等后处理工序。
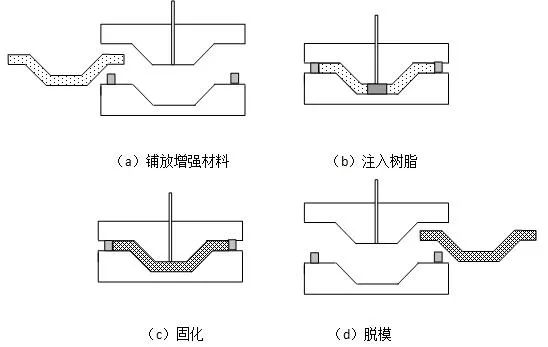
纤维预成型有手工铺放、手工纤维铺层加模具热压预成型、机械手喷射短切加热压预成型、三维立体编织等多种形式,需要达到的效果就是纤维能够相对均匀填充模腔,以利于接下来的树脂充模过程。 在合模和锁紧模具的过程中,根据不同的生产形式,有的锁模机构安装在模具上,有的采用外置的合模锁紧设备,也可以在锁紧模具的同时利用真空辅助来提供锁紧力,模具抽真空同时可以降低树脂充模产生的内压对模具变型的影响。 在树脂注入阶段,要求树脂的黏度尽量不要发生变化,以保证树脂在模腔内的均匀流动和充分浸渍。在充模过程结束后,要求模具内各部分的树脂能够同步固化,以降低由于固化产生的热应力对产品变形的影响。这种工艺特点对于树脂的黏度和固化反应过程以及相应的固化体系都提出了比较高的要求。 随着原材料技术、模具技术、设备技术的快速发展,RTM的生产布局也出现了多种多样的形式。 按照生产效率划分,可以将RTM工艺的发展划分为三代。第一代RTM工艺通常为常温固化或外部加热,生产周期在80~150分钟左右,其生产布局如图6-2所示。生产布局常采用环形生产线,模具在不同的工位流动,模具数量多,生产周期取决于时间最长的工序, 通常为固化工序。
第二代RTM工艺的特点是模具自带加热系统,同时采用了专门的开合模锁紧机构,生产效率可以达到20~30 分钟。图6-3所表示的是代表性的双工位RTM工艺布局,一个工位在喷射胶衣、铺放纤维时,另一个工位可以进行注射、固化过程。
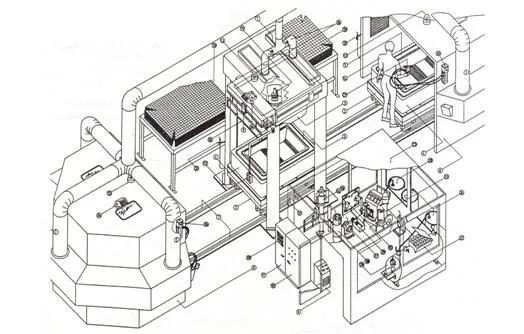
第三代RTM工艺采用的是120℃左右的固化温度,模具由专用的压机带动实现开模、合模、锁紧,设备采用高速注射设备,模具使用金属模具,整体布局和SMC工艺类似,成型周期小于10分钟。如图6-4所示。
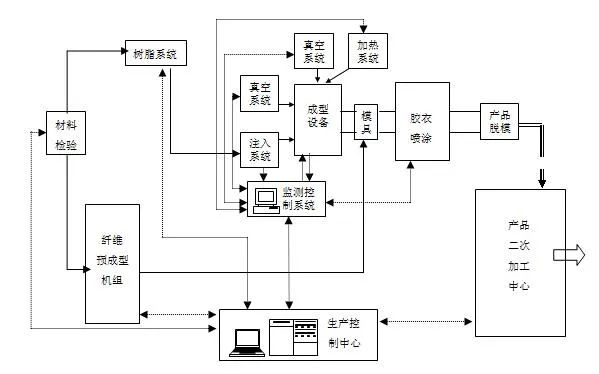
影响RTM工艺的工艺参数包括树脂黏度、注射压力、成型温度、真空度等,同时这些参数在成型过程中是互相关联和互相影响的。 (1) 树脂黏度 适用与RTM工艺的树脂应该具有较低的黏度,通常应小于600mPa•s,小于300mPa•s时工艺性会表现地更好。当所使用的树脂黏度较高时通常提高树脂和成型温度来降低树脂黏度,以利于更好地实现充模过程。 (2) 注射压力 注射压力的选择取决于纤维的结构形式和纤维含量以及所需要的成型周期。很多的研究资料都表明,较低的注射压力有利于纤维的充分浸渍,有利于力学性能的提高。通过改变产品结构设计、纤维铺层设计、降低树脂黏度、优化注射口和排气口的位置、使用真空辅助等手段,都可以实现降低注射压力。 (3) 成型温度 成型温度的选择受模具自身能够提供的加热方式、树脂固化特性及所使用的固化体系的影响。较高的成型温度能够降低树脂的黏度,促进树脂在纤维束内部的流动和浸渍,增强树脂和纤维的界面结合能力。有资料数据显示,较高的温度能够提高产品的拉伸强度。 (4) 真空度 在成型过程中使用真空辅助可以有效降低模具的刚度需求,同时促进注射过程中空气的排除,减少产品的孔隙含量。通过实验数据测定,在真空条件下成型的平板平均孔隙含量只有0.15%,而没有真空的平板孔隙含量达到1%。 随着应用领域的不断扩大,RTM工艺已经发展出了一系列的衍生工艺,代表性的工艺包括:Light-RTM、SCRIMP(Seemann Composites Resin Infusion Molding Process)、RFI(Resin film infusion)等。 Light-RTM通常称之为轻质RTM,该工艺是在真空辅助RTM工艺的基础上发展而来的。适用于制造大面积薄壁产品。该工艺的典型特征是下模为刚性模具,而上模采用轻质、半刚性的模具,通常厚度在6~8毫米。工艺过程使用双重密封结构,外圈真空用来锁紧模具,内圈真空导入树脂。注射口通常为带有流道的线型注射方式,有利于快速充模。由于上模采用了半刚性的模具,模具成本大大降低,同时在制造大面积的薄壁产品时,模具锁紧力由大气压提供,保证了模具的加压均匀性,模制产品的壁厚均匀性非常好。 SCRIMP成型技术是由美国西曼复合材料公司在美国获得专利权的真空树脂注入技术。与之类似的工艺有多种,但名称各不相同,以SCRIMP工艺最有代表性。其工艺原理是:在真空状态下排除纤维增强体中的气体,通过树脂的流动、渗透,实现对纤维的浸渍。成型模具首先将一层或几层纤维织物铺放于模具上,再放好各种辅助材料,然后用真空袋密封,开启树脂阀门吸注胶液,充满模具最后固化成型。 与传统的RTM工艺相比,它只需一半模具和一个弹性真空袋,这样可以节省一半的模具成本,成型设备简单。由于真空袋的作用,在纤维周围形成真空,可提高树脂的浸湿速度和浸透程度。与RTM工艺相反,它只需在大气压下浸渍、固化;真空压力与大气压之差为树脂注入提供推动力,从而缩短成型时间。浸渍主要通过厚度方向的流动来实现,所以可以浸渍厚而复杂的层合结构,甚至含有芯子、嵌件、加筋件和紧固件的结构也可一次注入成型。SCRIMP工艺适用于中、大型复合材料构件,施工安全、成本较低。 RFI首次是由L.Letterman(美国波音公司)申请的专利,最初是为成型飞机结构件而发展起来的。近年来,这种技术已改进了RTM中纤维含量低、模具费用昂贵、易生成缺陷等缺点。RFI也是采用单模和真空袋来驱动浸渍过程。工艺过程是将预制好的树脂膜铺放在模具上,再铺放纤维预成型体并用真空袋封闭模具;将模具置于烘箱或热压下加热并抽真空,达到一定温度后,树脂膜熔融成为黏度很低的液体,在真空或外加压力的作用下树脂沿厚度方向逐步浸润预成型体,完成树脂的转移;继续升温使树脂固化,最终获得复合材料制品。 (1) 不需要复杂的树脂浸渍过程,成型周期短,能一次浸渍超常厚度纤维层,具有高度三维结构的缝编、机织预制件都能浸透,并可加入芯材一并成型; (2) 树脂膜在室温下有高的粘结性,可粘着弯曲面; (4) 模具制造与材料选择的灵活性强,不需要庞大的成型设备就可以制造大型制件,设备和模具的投资低; (5) 成型产品孔隙率低(<0.1%),纤维含量高(重量含量接近70%),性能优异。 RFI工艺也存在一些不足之处,如:对树脂体系要求严格;不太适合成型形状复杂的小型制件;由于采用真空袋压法,制品表面受内模的影响,达不到所需的复杂程度及精度要求;RFI工艺中,树脂的用量不能精确计量,需要吸胶布等耗材除去多余树脂,因而固体废物较多。 在RTM模具中手工铺放增强材料是一件比较困难的工序。在铺放过程中,增强材料容易错位,同时增强材料的变型不能够与模具的型面变化相适应,需要手工剪开,然后粘接或缝合,这对于连续生产的一致性和效率都会产生影响。通过将纤维用一定的工艺手段预先制作成和模腔结构一样的预成型体,可以很好地解决这一问题。 RTM用的纤维类型包括E玻纤、R玻纤和S玻纤,以及各种高强高模碳纤维和芳纶纤维。所使用的玻璃纤维织物结构形式包括表面毡、机织布、短切毡、连续毡、缝编毡、多轴向织物、RTM专用复合毡以及立体编织物等多种类型。碳纤维等高性能纤维通常使用不同织造方法的布,在很多高性能部件的制造场合,三维立体仿形织物的应用越来越多。 方格布是最为常见的机织布,其它类型的机织布如斜纹布、缎纹布等都可以用于RTM工艺。各种类型的机织布在铺层时很容易发生皱折和扭曲,不容易铺放到位。因此机织布通常用于一些型面变化比较简单的产品,为保证纤维在模具内的稳定,可以使用特定的粘接剂固定织物,也可以采用手工缝编的方式,用涤纶线将布与布之间缝合在一起。 短切毡用于RTM工艺的优点是成本低,变形性好,缺点是耐冲刷性差,但是如果在靠近模具注射口的短切毡上面铺放机织布,可以降低树脂对纤维的冲刷。从实际使用的情况来看,短切毡和机织布配合使用可以提高制品层间的剪切性能,同时实现纤维在不同分布方向上的互补。 玻璃纤维连续原丝毡是一种重要的玻纤无纺增强基材,它是以一定数量的连续玻纤原丝随机分散成圈状均匀分布于网带上,靠原丝间互相交搭的连锁作用及少量粘结剂结合成毡。连续毡的单位面积质量为225~900g/m2,厚度为2~5毫米。由于连续毡具有各向同性、抗移性好、耐树脂冲刷、贴覆性好、制品强度高等优点,成为RTM工艺中非常重要的一种增强材料。 国外连续毡生产工艺主要采用“一步法”成毡技术,即在玻璃池窑拉丝漏板下布置多台成型工艺装置,通过数台抛丝机将纤维拉出并直接铺撒在行进的网带上形成毡坯,再经过施胶、烘干,收卷成毡。这种工艺的特点是纤维分散性好,产量大,自动化程度高。目前国际上“一步法”成型生产工艺以美国欧文斯科宁公司和法国圣戈班公司为代表。 缝编毡是通过缝编机将不同的类型纤维缝合成纤维毡的结构形式。缝编毡可以通过不同的缝合方式实行纤维织物多种增强结构形式,是RTM工艺中应用最多、成本较低的一种增强材料。各种缝编毡的类型包括: (1)单轴向织物 仅在与织物长度方向0(经向)或90(纬向)的一个方向平行铺设无捻粗纱并缝合成织物。 (2)双轴向织物 与织物长度方向成0、90、±45度的四个方向任意两个方向平行铺设无捻粗纱,每个方向各自形成独立的纱层并缝合成双轴向织物。 (3)多轴向织物 在与织物长度成0、90、±45的四个方向任意三个或四个方向上平行铺设无捻粗纱,然后缝合成多轴向织物。 (4)缝编短切毡 用组合在缝编机上的短切机,将无捻粗纱短切并铺撒均匀、然后缝合成毡。 (5)缝编复合毡 将单轴向织物、双轴向织物、多轴向织物中的任意一种与缝编短切毡在缝编机上可缝合制成2~5层缝编复合毡。 三维编织是通过长短纤维相互交织而获得的三维无缝合的完整结构,其工艺特点是能制造出规则形状及异形实心体并可以使结构件具有多功能性——即:编织多层整体构件。三维织物主要应用于对力学性能要求非常高的航空航天结构部件的制造。 编织工艺的原理是:由许多按同一方向排列的纤维卷通过纱线运载器精确地沿着预先确定的轨迹在平面上移动,使各纤维相互交叉或交织构成网络状结构,最后打紧交织面而形成各种形态增强结构的三维织物。 (1)异型件一次编织整体成型,实现了人们“直接对材料进行设计”的构想; 国外在纤维预成型体方面的研究、应用起步较早,涉及内容已相当深入、全面,并针对产品性能、功能和用途要求建立了一系列相适应的预成型体制备方案。已经研究开发的常用方法有三种:第一种方法是纺织、针织或编织净外形或接近净外形的预成型体;第二种方法是将增强材料缝合成弹性、半弹性的增强材料部件嵌入模具中;第三种方法是粘结预成型方法,对于某些具体的部件,它们常常可以独立或混合使用。纤维预成型技术在国外的工业产品中代表性的案例,如:Dowty航空公司用编织预成型方法成功生产了螺旋桨叶片;1987年美国福特四轮驱动轿车Aerostar横梁、福特P100皮卡后挡板预成型体采用了CFRM热冲压成型等。目前国外许多研究者们仍在预成型体粘接剂、制备方法、粘接剂对工艺及制品性能的影响等方面开展研究工作,并且在预成型体设计,预成型体变形性,渗透性,力学性能分析等多方面建立了理论,并逐渐向数字模拟分析,力学性能预测和流变性能预测的方向发展。PAM公司成功开发了PAM-Form预成型体分析软件,并做到与PAM-RTM的多物理场耦合分析,提高了复合材料制品性能的控制和预测能力。这些研究方向实际是RTM工艺和预成型体工艺工业化技术水平发展到目前的一种市场需求,反映了预成型技术在国外已经从RTM工艺需要的附属工艺流程中分离,逐渐形成一整套独立的成型工艺过程。 预成型体必须满足一系列的工艺要求才能保证复合材料制品的质量和性能,而这些都与增强材料的性质、织物结构、定型剂种类和预成型体制造工艺等密切相关。下面几方面是纤维预成型体所要求的工艺特性。 (1) 浸渗特征:纤维预成型体最基本的要求是树脂必须对它能充分浸渗,并且要在尽可能小的压力下和尽可能短的时间内完成这一过程。其中一个重要的浸渗参数是纤维预成型体的渗透率。渗透率与纤维预成型体的纺织结构有密切关系,特别是纤维的排列方向、纤维的体积分数和纤维对树脂浸润性等。 (2)纤维的浸润性:这种性能基于纤维和树脂的自由表面能,由它们的接触角决定的。为了使树脂充分浸润纤维,纤维的表面能必须大于树脂的表面能,因此商业用的纤维大都进行了表面处理,采用定型剂时,必需考虑树脂对含定型剂纤维的浸润性,通过定型剂处理能提高浸润性。 (3) 预成型体的抗冲刷性:对于纤维体积分数高的预成型体,为了提高浸渗速率,通常需要比较大的树脂注射压力,为保证纤维的排列方向不被冲乱,这就要求预成型体有良好的抗冲刷性,采用定型剂预成型时,保证定型剂有一定的粘接力和刚度。 (4)预成型体的均匀性:预成型体的各部分浸渗参数相差尽可能的小,以利于树脂能按照预计方向流动。因此制备预成型体时均匀分散定型剂很重要。 (5)预成型体的可操作性:预成型体的可操作性依赖于预成型体的刚性和预成型体的整体性,目的是使预成型体在工艺过程中易于操作而不会对纤维的排列和体积分数造成影响。 (6)预成型体的表面平整性:对于表面质量要求高的制件(如汽车零部件),预成型体的表面质量直接影响着产品的使用,有时还必须通过应用胶衣树脂才能达到使用要求。 短切纤维喷射预成型体制备方法,即经常提到的直接纤维预成型,短切纤维与粘结剂一起被喷射到开有预留孔的模板或网屏上(通常采用组合的粗纱和热固性树脂乳胶作为胶黏剂),喷洒完成后需将预成型体烘干,也可以采用粉末和纤维形式的热塑性胶黏剂。在传统工艺中,通过有孔模板吸入空气,在沉积纤维的同时保持或部分干燥预成型体。喷射完后,加热预成型体至胶黏剂固化定型。其工艺特点是原材料成本低,可以生产净形预成型体。但由于短切纤维力学性能低,限制了其应用范围;而且模具工装费用成本较高,能量消耗大。
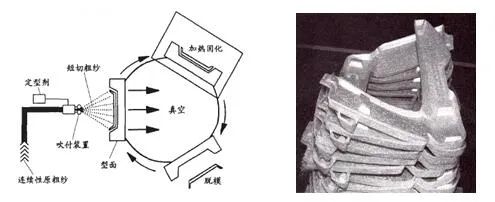
CompForm预成型是唯一能使用多种增强材料的成型工艺,能使用一种或几种增强材料混合成型。该预成型体工艺使用液态热塑性粘结剂,通过紫外线照射固化。由于这些胶粘剂由紫外线提供固化能,固化非常迅速且可通过几种方式实现。CompForm工艺的特点就是能制造复杂的预成型体,通过逐次的预成型或组合程序。这种预成型工艺制成的预成型件可包括夹心材料及嵌件。 由于粘结剂是热塑性的,可以实现稳定的工艺重复,或不止一步地进行预成型。逐次的组合,就像装配线上的焊接工艺一样,都能很容易地实现。另一方面,在选定部分可使用不透明的遮光罩,使得选定部分的粘结剂不固化以备后面的组装或成型用。被遮住没有固化的区域,允许复杂的形状被“展开”成简单的形状,经“再包裹” 成最终的形状,然后将前面的遮光部位用紫外线照射固化胶粘剂进行固化。 P4预成型体工艺项目受ACC(汽车复合材料国际联合组织)的Focal Project Ⅱ和Ⅲ的支持。是为了实现Focal Project Ⅱ为目的,即制备复合材料小吨位卡车轴承箱的SRIM模塑要求的高容量纤维预成型产品。 P4包括三种主要的步骤:纤维铺层、固化及预成型脱模。工艺的第一步是切碎纤维及粘结剂的附着。纤维粗纱被切碎后与热塑性粉末状粘结剂一起喷射到预成型模具上。通过表面的正向气流保证切碎纤维固定在模具表面。一旦喷射完成,模具锁紧,预成型体被压缩到所要求的厚度。然后向模具内吹热空气熔化粘结剂。粘结剂被熔化后,热气流停止,粘结剂固化使纤维定型。模具开模,完成预成型体脱模。与短切纤维预成型制备工艺比较, P4工艺从本质上和原理上并没有太大的区别。只在最后定型阶段上,P4工艺用到了对模压制方法,这样将有效保证纤维的体积含量,同时为预成型体提供足够的刚度,即能生产高度坚固,净外形/净尺寸的预成型体,而这仅需要通过适当的模具来实现,模具能将预成型体压缩到要求的厚度,同时也增加了整个预成型体的刚度和可操作性。净外形/净尺寸特征可通过真空消除玻璃纤维的过多喷涂,也可通过净边模具设计来满足分模边的确定。该净尺寸能省去修理操作的需要。 预成型工艺的自动控制与直接纤维预成型相比有几大优点:控制喷射程序提供了可重复性与零件的一致性;控制玻璃纤维附着能消除超量喷射,因此减少了玻璃纤维废料;自动控制配合高级切碎枪预计能提供在快的循环周期内喷射复杂形状。但P4预成型体工艺的可重复型是建立在完全自动化的机械上胶预成型工艺,整个工艺自动化通过机械手和自动机械控制来完成。
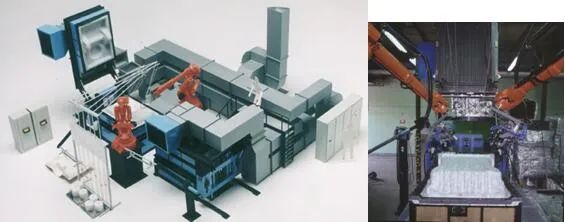
采用含有定型剂的片状增强材料,铺贴在模具上,通过加温、加压、冷却和脱模等工序,靠物理作用固定片状纤维。增强材料主要是织物和玻璃纤维毡。片状预成型分为热模压成型和直接成型。直接成型不需要预成型体;热模压成型是通过加热,熔化定型剂并加压成型的方法(见图6-7)。(1)增强材料的裁剪:把增强材料裁剪成比产品外形尺寸大10 cm的形状;在预成型模具里不加热条件下模压;切成所需的形状。(3)在加热模具里加热加压,温度和时间与定型剂有关,一般为110~150℃,60~180 秒。 其优点为适合形状单一的产品;周期短;可自动化。缺点为不适合深度大的形状;表面上易留增强材料的花纹;有10%的损失;易出现富树脂部位。
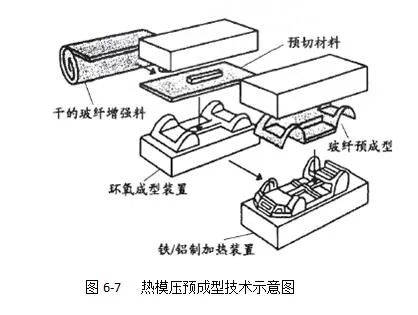
黏度:树脂黏度范围在0.1~1Pa•s,一般为0.12~0.5 Pa•s。黏度太高或太低可能导致浸渍不良,或形成大量的孔隙和未被浸渍的区域,影响制品的性能和质量。黏度太高的树脂需要较高的注射压力,容易导致纤维被冲刷。 相容性:树脂对增强材料应具有良好的浸润性、匹配性和界面性能。 反应活性:RTM工艺用树脂的反应活性应表现为两个阶段,在充模过程中,反应速度慢,不影响充模,充模结束后,树脂在固化温度条件下开始凝胶,并迅速达到一定的固化程度,这样才能减少模具占用时间,提高生产效率。 收缩率:树脂收缩率要低,树脂收缩率过大会增加孔隙率和制品裂纹的机会。 模量:在满足力学性能的前提下,树脂模量适中。高模量的树脂产生高热应力,容易引起制品变形和产生裂纹。 韧性和断裂延伸率:树脂这两个指标主要与制品抗冲击与耐裂纹性能成正比,较高值可提高树脂耐热裂纹的能力。 用于RTM的聚酯树脂用通用型、低收缩性以及其它一些特殊类型 (1)英国Joton Polymer公司生产的Norpol 42-10是一种中等活性、刚性的邻苯树脂。该树脂在23℃的物理性能为:黏度180~210mP•s,密度1.1g/cm3,胶凝时间12~18分钟。其性能列在表6-2中
性能 | 纯树脂 | 玻纤毡增强 | 性能 | 纯树脂 | 玻纤毡增强 |
纤维含量(重量)% |
| 25~30 | 35~40 | 拉伸强度/MPa | 140 | 155 | 215 |
拉伸强度/MPa | 70 | 110 | 160 | 拉伸模量/GP a | 3.6 | 7.2 | 10 |
拉伸模量/GP a | 3.7 | 8.0 | 10.3 | 冲击强度/kJ/m2 | 12 |
|
|
断裂延伸率/% | 3.5 | 2.0 | 2.2 | 热变型温度/℃ | 67 |
|
|
Norpol 42-96是一种中等反应性的不饱和聚酯树脂,特别适用于低压注射工艺和发泡注射工艺。Norpol 42-96树脂的发泡过程,是先加入1.25%的发泡剂Luper-Foam329,而后再加入3%的Luperox DP33促进剂。这种聚酯泡沫制品的密度,要比通用聚酯的轻得多。Norpol 42-96的胶凝时间约为9~14分钟, 含15%玻璃纤维毡复合材料的密度约为0.9~1.0g/cm3,抗拉强度为20~30MPa,抗拉模量为2.7~3.2GPa,抗弯强度为45~55 MPa,摆锤式冲击强度为31kJ/m2。当玻璃纤维含量为25%时,其密度约为1.0~1.2g/cm3,抗拉强度为60~70 MPa,抗拉模量为6.3~7.2GPa,抗弯强度为100~110 MPa,摆锤式冲击强度为46 kJ/m2。 Norpol 80-1-06阻燃型树脂,是用于树脂注射工艺的一种自熄式快速固化的聚酯树脂。其玻纤增强制品,根据英国标准BS476Part7测试标准,符合自熄性要求。该树脂黏度较低,能快速浸湿玻璃纤维增强材料。 (2) 意大利Alusuisse公司的RTM工艺用树脂Disititron 21182和Disititron 441,可以满足用户的不同要求。其性能列于表6-3
表6-3 Disititron树脂的性能
性能 | DS 21182 | DS 441 | 性能 | DS 21182 | DS 441 |
黏度(25℃)/mP.s | 700 | 450 | 拉伸模量/GPa | 3.8 | 3.6 |
纤维含量(重量)% | 30 | 35 | 断裂延伸率/% | 2.5 | 3 |
凝胶时间(75℃)/s | 170 | 210 | 弯曲强度/MPa | 100 | 130 |
热变形温度/℃ | 95 | 75 | 弯曲模量/GP a | 3.7 | 3.8 |
拉伸强度/MPa | 60 | 70 |
|
|
|
(3)金陵帝斯曼树脂有限公司生产的RTM树脂主要有三个牌号,其性能见下表,其中以P6-988KR最为常用。
品牌 | 产品牌号 | 类别 | 黏度 | 凝胶时间 | HDT | 拉伸强度 | 断裂延伸率 | 特性及说明 |
Synolite | 1777-G-4 | 邻苯 | 185 | 28-31 | 91 | 80 | 4.1 | 用于真空辅助注射成型,优良的浸润性能,适合制造结构复杂制品 |
Synolite | 4082-G-22 | 邻苯 | 185 | 9-15 | 63 | 70 | 2.0 | 机械性能好,玻纤浸润优良,固化性能好,放热峰低,中国船级社认证 |
Palatal | P6-988KR | 邻苯 | 325 | 15-25 | 70 | 70 | 3.5 | 高延伸率、高冲击强度、流动性好 |
德国BASF公司的Palapreg R30-01V低收缩树脂,可以达到A级表面质量。只要工艺条件合适,该系统可适用于各种RTM用途,不管是否使用胶衣,都能获得良好的表面质量。RTM成型时,模具的最低温度为60℃,最佳温度为80℃。当模塑制品在常温下固化,放置24小时后,制品的收缩率约为0.11%。若制品在80℃下固化,放置24小时后,尺寸则没有变化。成型的复合材料性能为:弯曲强度175Mpa,弯曲模量7Gpa,拉伸强度120Mpa,冲击强度80KJ/m2。 美国Ashland Chemical公司生产的Arotran树脂, 由于采用了新的聚酯化学技术,可用于制造A级汽车覆盖件。该树脂的模塑温度为60℃,聚合反应中出现的物理微孔,可消除收缩,从而得到光滑表面。 其配方和工艺条件为;100份树脂,70份碳酸钙和2份Luperso/DDM-9。增强材料包括一层表面毡,24 %的连续纤维毡及定向布毡,RTM注射机的气压为275-550KPa,树脂与过氧化物的比率为100:1.2。 乙烯基树脂是用环氧树脂和不饱和酸反应制成的,其分子链末端具有高交联度、高反应活性的双链,化学性能稳定,其中稳定的苯醚键使乙烯基树脂耐腐蚀。另外,酯基只位于分子链端部,固化反应时交联也只在端部进行,整个分子链都不参加反应。因此,分子链可以拉伸,并表现出比较好的韧性,延伸率可以达到4%~8%。由于乙烯基酯独特的分子链和合成方法,使其固化物的力学性能接近环氧,工艺性能类似聚酯。具有高度耐腐蚀性。它的耐酸性能优于胺类环氧,耐碱性优于酸类固化环氧和不饱和聚酯。乙烯基酯分子中的羟基,增加了树脂对玻纤的浸润性。Dow化学工业公司生产的Derakane牌号的乙烯基酯树脂可用于RTM工艺。
树脂体系 | 说明 | 黏度/Mp.s | Tg/℃ | HDT/℃ | 断裂延伸率/% |
Derakane411C-50 | 双酚A乙烯基酯树脂 | 125 | 240 | 215 | 5~7 |
Derakane 530 | 溴代双酚A环氧乙烯基酯树脂 | 450 | 270 | 230 | 4~5 |
Derakane510A-40 | 溴代双酚A环氧乙烯基酯树脂 | 250 | 260 | 230 | 4~5 |
Derakane 470-36 | 酚醛型环氧乙烯基酯树脂 | 200 | 305 | 300 | 3~4 |
Derakane 8084 | 韧性双酚A环氧乙烯基酯树脂 | 375 | 230 | 180 | 8~10 |
XU71835.OIL | 高韧性交联乙烯基酯树脂 | 350 | 250 | 200 | 6~8 |
国内乙烯基树脂比较有代表性的生产企业是上海华东理工大学华昌聚合物有限公司 ,该公司生产MFE系列的乙烯基酯树脂。
表6-6 MFE-RTM-200树脂浇铸体力学性能
检验项目 | 检验结果 | 测试方法 | 检验项目 | 检验结果 | 测试方法 |
拉伸强度MPa | 63.94 | GB/T 2568 | 弯曲模量GPa | 3.39 | GB/T 2570 |
拉伸模量GPa | 2.75 | GB/T 2568 | 压缩强度MPa | 108.68 | GB 2569 |
延伸率% | 4.22 | GB/T 2568 | 冲击强度KJ/m2 | 12.42 | GB 4493 |
弯曲强度MPa | 126.38 | GB/T 2570 | 热变形温度℃ | 105 | GB 1634 |
环氧树脂主要用于成型高性能复合材料,一个环氧树脂体系是否能适用于RTM成型,是否能成为高性能复合材料的树脂基体,不仅与环氧树脂品种有关,同时亦取决与所用固化剂及促进剂。为使树脂体系适用于RTM成型,固化剂体系在室温下应为低黏度液体,与环氧树脂配合后树脂在注射温度下具有良好的储存稳定性,固化树脂具有良好的耐热性、高强度、高韧性。目前常用的固化剂为液体胺类和多官能团的液体酸酐等。 针对高性能环氧树脂体系工艺性差的问题,另一个解决的方法是通过升温或加入稀释剂。但升高温度将缩短工作期,而活性稀释剂在有效降低体系黏度的同时又常常降低制品的耐热性。所以,开发研制耐高温活性稀释剂也是环氧树脂体系改性的一条重要途径。 适用于高温成型工艺的代表性环氧树脂主要有Ciba-Geigy公司开发的LSU940/XU205和3M公司开发的PR 500环氧树脂体系,主要应用与航空复合材料制件。室温成型用环氧树脂通常是双组分的,由环氧树脂和室温下黏度较小的固化剂组成。代表性的有CYTEC公司的CYCOM 823和HEXCEL公司的RTM6。国内比较有代表性的室温注射RTM树脂有北京航空材料研究院研制的3266环氧树脂体系。3266是一种80℃固化120℃后处理、中温75℃长期使用的结构性RTM专用环氧树脂,主要应用在高动态载荷的部件如飞机螺旋桨桨叶、舰船或鱼雷推进螺旋桨桨叶以及其他主承力结构上。
测试项目 | 3266 | CYCOM 823 | RTM 6 |
密度(g/cm3) | 1.2 | 1.23 | 1.14 |
拉伸强度/MPa | 80.58 | 80 | 75 |
拉伸断裂应变/% | 6.5 | / | 3.4 |
拉伸模量/GPa | 3.47 | 2.9 | 2.8 |
弯曲强度/MPa | 151.4 | 144 | 132 |
弯曲模量/GPa | 3.77 | 3.4 | 3.3 |
干态Tg/℃ | 120(DSC) | 125 |
|
双马来酰亚胺树脂力学性能好,高温稳定性突出,低毒、低烟。主要缺点是黏度高、韧性差。用于RTM工艺需要改性,主要采用自由基共聚、Michael加成、Diels-Alder反应等手段获得。国外代表性树脂有Ciba-Geigy公司开发的Matrimid 5292,Technochemie公司生产的Compimide 65 FWR,DSM公司开发的Desbimid RTM树脂。 国内典型的双马来酰亚胺树脂有中国航空第一集团复合材料特种结构研究所用于RTM工艺雷达天线罩的F.JN-5-02,北京航空工艺研究所开发的QY8911-Ⅳ等。 该类树脂主要用于航空航天领域用的耐高温复合材料结构部件。 RTM工艺过程包括树脂充模流动、热传递和固化反应。其中热传递和固化反应是其它复合材料工艺所共有的,工艺控制重点是充模流动问题。 在RTM充模过程中,模具型腔内填充着纤维预成型坯,可以称之为纤维床,其中包含固体相——纤维和流动相——空气。树脂的充模过程就是保证树脂流过这些不规则的孔隙并将空气置换出去,使树脂充满孔隙的过程。树脂在这些不规则的孔隙中流动是非常复杂的,同时存在两种类型的流动,一种是纤维束间的宏观流动,另一种是纤维束内的微观流动。这两种流动在充模过程中相互竞争,可能导致浸润不良或气泡的包裹。 当注射压力较低时,纤维束内的毛细作用力起主要作用,流体的流动前沿形态如图6-8(a)所示,纤维束内的流动前沿领先于纤维束间的流动前沿,当领先的流体前沿沿横向流动汇合时,纤维束内未被排出的空气即被包裹,形成纤维束间的大气泡;反之,当注射压力较高时,毛细压力同动力压力相比作用较小,因而纤维束内流体的流动前沿落后于纤维束间的流动前沿,如图6-8(b)所示。当流动前沿横向流动汇合时,形成纤维束内部的小气泡。气泡含量是复合材料质量的重要指标之一。气泡的存在使纤维浸润程度低、粘结性差,使复合材料部件的机械强度不一致及表面质量低劣;同时易引起应力集中,引发裂纹的产生,降低了复合材料的耐久性、抗疲劳性及耐候性等。
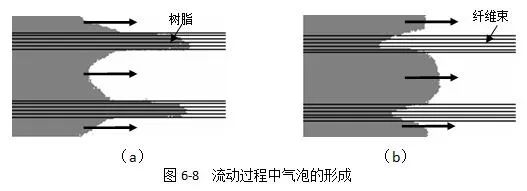
气泡形成制品的微观缺陷,主要存在于纤维束间或纤维束内单丝间,而干斑的产生则是制品的宏观缺陷。处理纤维预成型体时,经常出现预成型体弯曲、织物边缘松散、局部预成型体渗透性能变化等问题。在裁剪预成型体时,一般很难达到精确的尺寸精度,纤维束的松散性会使边缘处的纤维体积含量减小。此外,当模具设计不合理或合模不当时都容易使预成型体和模腔壁间及拐角处产生缝隙,而这一缝隙则形成了树脂的优先流道,树脂在这种通道中的流动超前于在预成型体中的流动,破坏了正常的流动前沿模式,这种效应称为“边缘效应”或“流道效应”。这类由于预成型体受剪切、压缩或者压紧效应,尤其是边缘效应引起的增强材料性能变化对充模过程有重要的影响,易引起纤维浸渍不充分、干斑等问题。一般的流道效应区为毫米级,在有些情况下,1~2mm的竞流区对充模过程也会有相当大的影响,使制品产生大面积的干斑。 对RTM工艺充模过程的分析研究都是建立在流体流经多孔介质的理论基础上,采用达西定律为动量控制方法。达西定律由Henry Darcy 于二十世纪中期根据一系列是实验结果提出的,在土壤学中有着广泛应用。达西定律中描述,流体流经多孔介质的速度与所施加的压力梯度成正比,而与流体的黏度成反比。达西定律是动量平衡方程的特殊形式,可以直接代入连续方程,而得到关于压力的控制方程。 对于水平流动,不计重力的情况下,达西定律可表达如下:
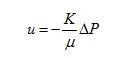
其中,u(m/s)为流体的速度矢量,K(m2)为预成型体的渗透率张量,为预成型体的内在属性,μ (Pa⋅s)为流体的黏度,以及 P (Pa/m)为压力梯度。可以看出,达西定律是一种体积上的平均描述,流体和纤维预成型体之间所有的复杂的相互作用都依靠渗透率张量来体现, 渗透率是描述充模过程中流体的流动特性的关键参数,获得准确的渗透率数据对于获得和实际生产相一致的模拟结果起着重要的作用。对于各向异性多孔介质,渗透率张量可表达如下:
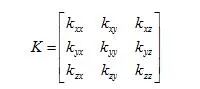
对于特别的正交各向同性预成型体,当局部坐标与纤维预成型体的主方向一致时,其渗透率张量可描述为:
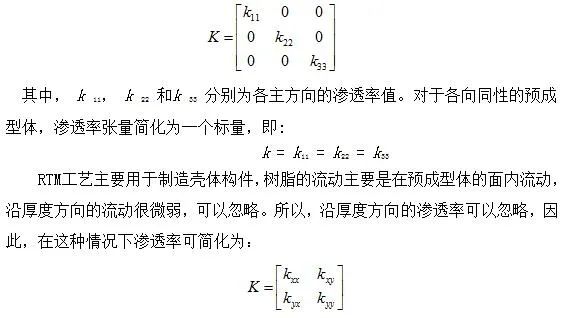
RTM 应用中纤维预成型体渗透率通常由三个途径获取:实验测量,解析求解和数值估计。
RTM工艺的流动模拟可以定性的预测树脂流动过程。如果输入的参数合理可靠,注射压力、流动速率、流动状态等可以通过模拟准确预报。建立分析技术的核心问题是如何获得输入的重要参数数据,如渗透率、树脂化学流变特性、热扩散以及边缘流动等。这些参数与复合材料的树脂体系、增强材料体系、模具以及工艺等都有紧密的联系。 液体流动过程有限元模拟理论是当今模拟技术的难点和热点,目前关于树脂流动的有限元模拟软件已趋于成熟,如荷兰Polyworx公司开发的RTM-Worx、法国ESI公司开发的PAM-RTM和美国MoldFlow公司开发的MOLDFLOW等。应用这些流动模拟系统,参照实际产品的使用要求、性能要求和成型工艺等参数,建立实际产品有限元模型,可以有效模拟产品的生产过程,指导实际产品的生产。 通过流动模拟技术在实际产品生产过程中应用的研究,可以得出流动模拟技术工程化应用的一般性流程:(1)对制件进行计算机几何建模,并借助有限元方法对模型进行有限元剖分;(2)根据制件的几何形状选择若干种可行的树脂注射方式;(3)选择和测定树脂流动模拟所需的各个参数,包括注射压力、预成型体的渗透率和纤维体积含量,以及树脂黏度等;(5)综合考虑树脂流动时间和最后填充位置,以及工艺操作的难易程度等各种因素,选择最优的树脂注射方式,指导实际生产。下面是运用RTM-Worx软件对天线罩RTM工艺充模过程进行模拟的例子。制件的几何形状及尺寸如图6-9所示。
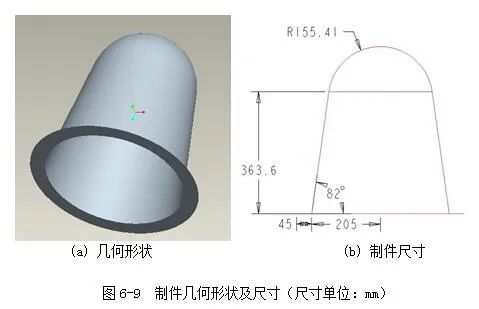
模拟时注射压力设为0.5MPa,假定增强材料预成型体各向同性、渗透率为1×10-10m2且分布均匀,纤维体积含量为40%,球冠和工作区的厚度设为14mm,圆环处的厚度设为20mm,树脂黏度设为0.4 Pa•s,模拟结果如图6-10所示。
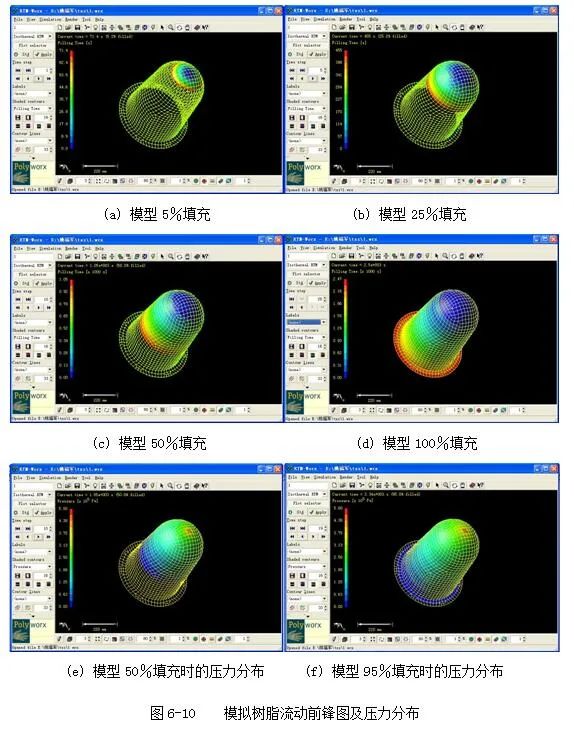
树脂注射设备包括加热恒温系统、混合搅拌器、计量泵以及各种自动化仪表。注射机按混合方式可分为单组分式、双组分加压式、双组分泵式、加催化剂泵式4种。现在用于批量生产的注射机主要是加催化剂泵式。 瑞典的Aplicator公司制造的RI-2设备,使RTM工艺朝高质量、高速度的全系统生产方面迈了一大步。它既可以用于制造高玻璃纤维含量的结构件,也可以生产A级表面的汽车部件。RI-2有1个单冲程液压泵,2个输送气缸,1个用于输送树脂,1个用于输送催化剂。有1个专用的输入阀直接将泵和模具连接起来,混合料就由该阀流进,没有溶剂和树脂暴露于工作区。该系统及喷枪都由1台程控机PLC)控制。所有的注射参数都可预先设定,供生产选择。注射在一个连续的冲程内进行,这可避免传统活塞泵中因压力下降以及流量脉动所引起的问题。控制注射既可以用压力,也可以用流量。通过一个在喷枪或模具内的压力传感器,可以在注射过程中以设定的压力注射。
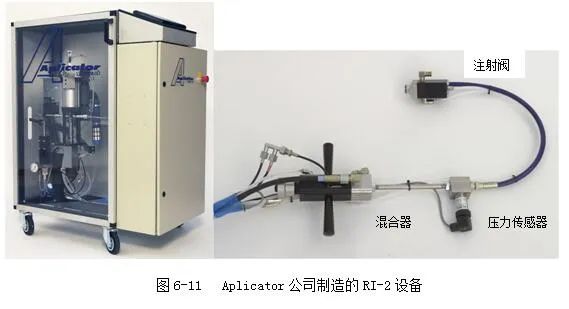
美国液控系统公司(LIQUID CONTROL SYSTEMS)制造的Multiflow RTM设备,可对从几克到数百公斤的反应树脂体系进行计量,混合并注射进低压力闭合模。这种机器的特点是有一台Posiload正向转换活塞泵,它使黏度的测量精确达±0.1~0.5%,且在温度、压力或材料黏度变化时不受影响。这种泵没有大多数泵采用的输入检验阀,通过真空辅助,可确保计量管完全充满料。 Multiflow CMFH型用于制造大型增强材料部件,输入量为45KG/min。可适用于多种树脂体系,包括聚酯、环氧,聚氨酯和甲基丙烯酸树脂。它可以注射未稀释的MEKP和BPO乳剂。使物料中催化剂浓度达0.5%。泵压力比从1:1到200:1。该机可处理的填料很多,包括碳酸钙、氢氧化铝以及空心玻璃微珠,计量精确度不受闭模引起的反向压力的影响。
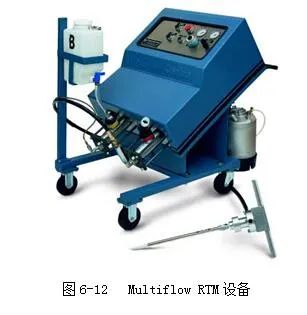
美国Glas-Craft公司生产的LPI型注射机,在国内引进较早,是一种相对简单的注射设备。该系统的特色为在18913—00型11:1的物料泵上安装了SP-85催化剂伺服泵。催化剂和树脂以容积计量,通过LI喷枪进行混合和分配。 18913-00型是一种双球往复式泵,即使在低操作压力下,它也有输出能力,来满足物料的需求量。它采用一个13cm直径的气缸,行程为10cm,能达到的最高传递速率为9.5L/min。SP-85催化剂泵是一个不锈钢正向置换泵,可在0.5~4.5%范围内准确分配催化剂。它有一个紧固的联动机械,可以很容易地调节微量的催化剂百分量。LI内混合喷枪的特色在于有一个新颖的混合头和18cm长的静态混合管。它们组合在一起可以使树脂和催化剂在低压下得到很好的混合,保证制品均匀、连贯的固化。这套系统还有一个催化剂流量监测器,如果分配时流体压力偏离正常设定值,报警器响,系统被切断。
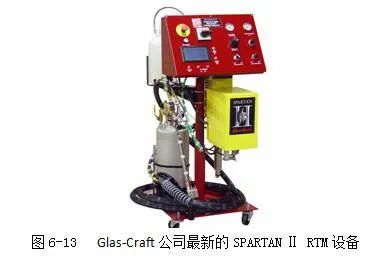
英国P1astech TT公司生产的注射机考虑到了多种生产参数的集中控制问题,是一种很有特色的低压连续注射树脂设备,其中Megaject Pro型是自动化程度最高的一种(见图6-14),主要特点为: (1)系统的工作控制全部通过一个液晶触屏面板来完成,屏幕界面分为管理员界面和用户界面,并采用密码保护。可以为多个模具设定注射工艺参数:注射量,注射压力,引发剂用量、加热器温度等,并实现注射全过程的一键控制。 (2)注射枪头位置设置树脂压力传感器(MPG),通过MPG可以根据设定的压力控制注射速度,防止产生比实际工艺要求高得多的压力。 (3)引发剂泵的调节采用电机控制,可以根据设定参数在工作过程中变化,保证了树脂在模内引发同步。引发剂流量检测装置会以曲线的形式给出实际流量,当偏离设定值时,就会报警。 (4)自动凝胶系统在注射结束后开始计时,在过了安全期后,报警器就会发出警报。继续注射,报警器复位但不取消,要取消它,需启动自动清洗键,用溶剂清洗混合器。 (5)特殊的喷枪空气清洗控制器,它可以减少清洗剂的用量,减少污染,使其再被利用,同时空气清洗也使混合器得到干燥,避免了混合器受污染。 (6)Megaject配装一个气动真空器,使用者可以方便地控制操作,为模具提供真空。
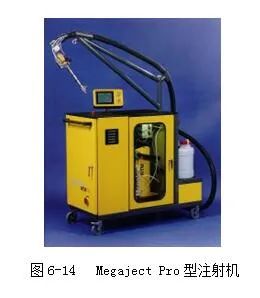
RTM是在低压下成型,模具刚度相对要求低,可以使用多种材料来制造模具。常用的模具类型有玻璃钢模具,电铸镍模具、铝模具、铸铁模具和钢模。表6-8列出了各种类型模具的比较。
表6-8 不同类型的模具比较
| 玻璃钢模 | 电铸镍模 | 铝模 | 铸铁模 | 钢模 |
强度/MPa | 150~400 | 300 | 50~500 | 100~200 | >300 |
模量/GPa | 7~20 | 200 | 71 | ~150 | 210 |
韧性 | 冲击引起损伤 | 耐低冲击 | 易造成划痕 | 不易损伤 | 不易损伤 |
密度g/cm3 | 1.5~2 | 8.9 | 2.7 | 7.2 | 7.8 |
热膨胀系数×10-6℃ | 15~20 | 13 | 23 | 11 | 15 |
热导率/W·m-1·K-1 | ~1 | ~50 | 200 | 70 | 60 |
比热容/ J·kg-1·℃-1 | ~1000 | 460 | 913 | 500 | 420 |
最高使用温度/℃ | 80 | >树脂固化温度 | >树脂固化温度 | >树脂固化温度 | >树脂固化温度 |
公差 | 固化收缩变形 | 取决于原模 | 精度高 | 精度高 | 精度高 |
表面光洁度 | 可抛光 | 抛光改善光洁度 | 抛光改善光洁度 | 不如铝和钢模 | 抛光改善光洁度 |
修复 | 胶衣损坏容易修复,增强层损坏难修复 | 不易修复 | 容易 | 容易 | 容易 |
制造周期 | 2~4周 | 30~40天 | 30~40天 | 30~40天 | 30~50天 |
RTM模具的结构设计包括产品结构分型;嵌模、组合模、预埋结构、夹芯结构等模具结构形式;专用锁紧机构、脱模机构、专用密封结构;真空结构形式;模具层合结构、刚度结构形式、模具加热形式等。(1)尽量简化脱模部件:在制造模具时应考虑产品脱模,覆盖件两边缘要留有一定的脱模角度,各部分的连接处平滑过渡。(3)便于气体排除:为了有利于气体的排出,分型面尽可能与树脂流动的末端重合。(4)模具密封和真空辅助成型:模具采用双密封结构并且利用真空在浸渍前对模腔抽真空,这样有利于降低模具变形、降低孔隙率、提高生产效率、减少修整工序。(5)便于活块的安放:当分型面开启后,要有一定的空间便于活块的安放,并保证活块安放稳固,覆盖件模具的活块采用真空吸附,利于定位和稳固。(6)模具制造的难易性:模具总体结构简化,尽量减少分型面的数目,采用平直分型面。
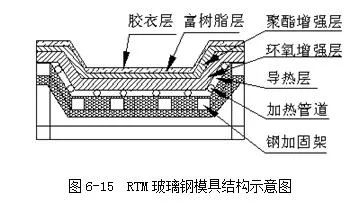
(1)中心位置:注射口选择在产品的几何形心,保证树脂在模腔中的流动距离最短。 (2)边缘位置:注射口设计在模具的一端,同时在模具上设有分配流道,树脂从边缘流道注射,排气口对称地设计在模具另一端。 (3)外围周边:树脂通过外围周边分配流道注射,排气口选择在中心或中心附近的位置。虽然外围周边注射的流道也在边缘,但它是闭合的,排气口在模具的中心处。 无论怎样选择注射口的位置,目的都是保证树脂能够流动均匀,浸透纤维。在模具上设有多个注射口可以提高注射效率,但是要保证不同注射口在流动边缘到达下一注射口时,该注射口能够及时开启,上一注射口及时关闭,避免出现断流或紊流造成的流动死角。 排气口通常设计在模具的最高点和充模流动的末端,以利于空气的排出和纤维的充份浸润。借助流动流动模拟软件可以比较好地确定理想的注口和排气口。 模具的密封通常采用不同结构形式的密封条来实现,所用到的密封条结构有O型、矩形和异型密封条,材质使用硅橡胶比较好。为了保证模具的有效密封和模腔内抽真空的需要,经常会用到双密封结构。 在RTM工艺中对模内树脂的加热方法有两大类:一是直接加热法。如美国RP/CMachinery 公司将射频电能直接通到型腔内的树脂中使树脂固化,该方法较先进,热效率最高,但难度大,目前还不成熟;二是间接加热法:热能由介质(气、水、油、蒸汽)携带,经模具背衬、型壳、型面传导到树脂中,使树脂固化。间接加热法分为三种。 (1)背衬管路法。模具背衬里铺设热介质的管路(循环管路),由于管路离型面有一定距离,而复合材料属热的不良导体,热传导较困难,因此加热速度慢,加热循环较长。应用此方法要求改善模具材料的导热性,且选择较平坦的产品类型,以便铺设管路方便易施。 (2) 型壳管路(或电热丝布)法。型壳里贴近型面铺设热介质循环管路 (或电热丝布)、热介质流的控制与压机、模具周边夹紧的操作相协调。1个供热系统可同时供多个模具,加热、冷却的速度最快,但每个模具的成本最高。 (3) 整模加热法,物料充模后,将整个模具置于固化炉(或高压釜)内加热,热能经过模具传导到型腔内的树脂,致使树脂固化,要求模具材料的导热性好,固化炉内能容纳整个模具,如果固化炉尺寸较大,可同时加热多个模具,本法加热效率低、固化周期长。 另外美国Sterling Heights公司研制高速RTM工艺,采用钢模具、模内有管路、管内通140℃左右的蒸汽,45秒树脂固化、再配以其他“高速技术”,如预混合、预催化、特殊单一树脂、快速投料、快速注射等,模塑周期约1分钟。
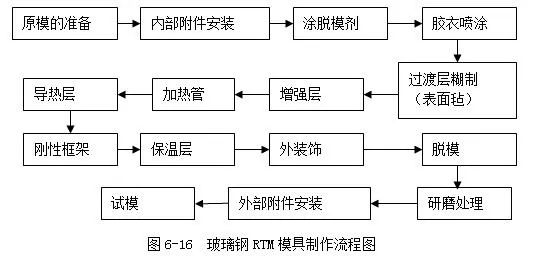
原模的准备工作中最重要的一项是检验工作。复合材料的成型是不可逆的,所以每做一工序都需要检验验证其正确合格方可进行下一道工序的施工,这也是保证模具制作出现问题时及时调整,把损失降到最低的最有效的方法。 内部附件包括注入口嵌件,排气口嵌件,密封条,辅助模内顶出件,模内导向定位件以及产品预埋件定位机构等等。 胶衣层是保证模具表面的基础,厚度宜在0.5~1.0mm,可分2~3次喷涂,固化时间以手触判断,触觉粘而指尖未带有胶衣为宜。过渡层可用30-50g/m2表面毡糊制,糊制过程中保证不能有气泡存在,固化后开始糊制增强层,糊制过程中最主要控制铺层的均匀程度及含胶量均匀程度。 对于形状简单、面积较大平板类型的模具,可以在增强层采用毡布交替的铺层设计方式,此方法可以进一步提高板壳强度,而曲面较多,形状复杂的模具直接由短切毡铺层糊制即可。但根据不同的模具质量要求慎重选择布类增强,因其强度和含量存在方向性,容易导致模具出现因收缩不均而引起的翅曲变形。 另外,根据不同的树脂体系和不同的模具要求及糊制制度进行操作,一般情况下,每固化一次糊制的层数越少,模具尺寸精确度较高,模具强度低,模具变形机率较小;相反每固化一次糊制的层数越多,整体强度较大,收缩变形机率也较大。 有加热层设计的模具,增强层的制作厚度应为6~8mm,既保证表面强度,其隔热作作也不至过于突出。加热层由加热管路和导热介质构成,加热管路采用铜管制成,并贴附于增强层的表面,先局部固定后,再用导热材料浇铸成型。 模具的加固要使用金属等刚性材料,按板壳理论设计结果确定平板单元区域大小并进行网格式加固,框架焊接完成后必须进行去应力处理,糊在模具背后使其与模具粘接成为一体。有加热层的模具还要在最后制作保温层,根据保温材料的不同,保温层厚度一般为50~100mm,浇铸成型。 随着材料技术和工艺技术的不断发展,RTM工艺制品已经在航空航天、交通运输、体育用品、船舶、建筑等领域得到了广泛的应用。由于RTM工艺的特点,在大型部件和高结构性能要求的部件制造方面其工艺优势更为突出。
应用领域 | 典型部件 |
航空、航天、军事 | 通道壳体、门;控制面板;防冻管道部件;驱动轴;电器盒;发动机罩上的支撑;风扇叶片;机翼;燃料贮罐;直升机驱动轴;型杆;红外线跟踪装置底座;发射管;军事装备盒;导弹体;碳/碳部件制造体母模;螺旋桨;天线罩;转轮叶片;盔甲片;静叶片;太空站支柱;军用品配件;换向器部件;鱼雷壳体以及水下武器原型等 |
汽车 | 车体外壳;保险杠;货箱顶蓬;变速器;底盘交叉部件;前后底盘零件;板簧;载货车厢;平底缸式底盘;空间框架等 |
建筑 | 柱子、标杆、商业建筑的门、框架、施工现场的脚手架、公用电话亭、人孔盖子、标志牌 |
电器 | 办公设备底座、传真机底座、计算机工作台面、抛物线型盘碟、天线罩 |
工业 | 冷却扇叶片、压缩器机壳、防腐蚀设备、驱动轴、电力除尘器、地板、飞轮及飞轮系统部件、减速器、检验孔、混合用叶片、防护帽、RTM机器底座、日光反射器、模具栏杆、阀门管 |
船舶 | 船体、小船舱以及零部件、甲板、码头支撑柱、紧急避险装备及底座、螺旋桨、雷达桥、船桅 |
体育运动器材 | 游乐车、自行车架、把手、高尔夫车、高尔夫球棍、雪橇板、帆板、溜冰板、地板、游泳池 |
在该领域的应用主要大型结构部件的整体成型方面,应用实例见表6-10和6-11。
表6-10 (国外)RTM成型技术在航空航天领域的应用
部件名称 | 应用领域 | 厂商 | 技术特点 |
雷达罩 | RAF“狂风”超音速变后掠翼战斗机 |
| 以编织或机织纤维为增强材料,其纤维质量含量达60% |
飞机和气垫船螺旋桨 | Fokker F50、Saab S340、Bell LCAC 气垫船、Gruman追踪者、Piper Cheyenne IV | Dowty航空公司 | 轻质、低成本 |
正弦波杆、发动机入口的密封管、机身框架 | F-22、F117-A战斗机 | 美国Dow-UT公司 | LCM构件的结构性能可与预浸料构件相当或更高,且孔隙率更低,每架飞机的成本节省25,000美元以上 |
隔仓门 | 波音客机 | BP公司 | 采用金属对模成型,由6件碳纤维/环氧树脂的组合构件取代了40片铝材组合构件。 |
进气道、风扇出口护罩、推力反向器和叶栅等 | 飞机 | Dow-UT公司 | 复合材料结构件取代了昂贵的钛金属构件成功地应用于发动机和机舱构件,已取得联邦航空局的认证。 |
方向舵、整体机舱、螺旋桨叶片等 | Bell/SumSung直升机 |
|
|
机翼 | 飞机 | 波音公司 | 该工艺已广泛应用于制作大型、复杂型面、带加强筋条乃至带加强墙和梁的结构件。 |
表6-11 RTM成型技术在舰船和装甲车辆上的应用
部件名称 | 应用领域 | 厂商 | 技术特点 |
船用防护板 | 舰船 | Hardcore FRP公司 | 具有足够的强度和刚度,完全可以承受住3000t排量船只的撞击,但它比同样大小的钢制板减重近2700kg |
上层结构板(长20m、面积100m2) | 军舰 |
| 产品重2吨,利用两块10m×50m的真空工作台面,铺放35层800g/m2玻纤粗纱,20分钟注入740kg含预促进剂、热变形温度高的乙烯基树脂,35分钟凝胶。玻纤含量72%,孔隙含量<1%,树脂利用率高达95%。此外,在成型工艺过程中在军舰壳体层压板里嵌入铜丝网层,能够实现电磁屏蔽功能 |
框架 | Manta Test Vehicle(MTV) | 美国海军NUWC纽波特分部 | 框架由乙烯基酯树脂SCRIMP工艺增强E玻纤制成(具有海上侦察、水下搜索和测量、辅助通讯/导航及潜艇跟踪四种能力) |
船舶结构件 | 船舶 | Hinckley公司 | RFI工艺对树脂基体的工艺性要求较为苛刻,树脂在室温环境中应具有很好的成膜性,所成薄膜(厚度通常为500μm-1mm)能任意弯曲而不脆裂 |
船舶结构件 | 英国的Sandown级扫雷艇,瑞典的“Visby”隐身轻巡洋舰和“Skjold”隐身巡逻快艇,美国DD21“Zumwalt”级隐身驱逐舰 |
| 与传统复合材料成型工艺相比,LCM工艺在成型大厚度、大尺寸制品时具有突出优势,例如:一块19.5m长、3m宽的潜艇壁板在45min之内就可以成型完毕。 |
ACAVP车体 | 欧洲第一辆全复合材料车体装甲战车——ACAVP(Advanced Composites Armored Vehicle Platform)战车 | 英国 | ACAVP车体全部由E-玻纤复合材料与陶瓷材料经柔性袋RTM(Soft-Sided Resin Transfer Moulding)工艺整体模塑而成,与普通的装甲车辆相比,ACAVP重量更轻且防护水平更高。战车整体减重达25%,同时又能防止雷达信号和热信号探测,还具有降噪、隔热、阻燃、防碎片等性能,实现了较好的防护能力和机动性能的统一。 |
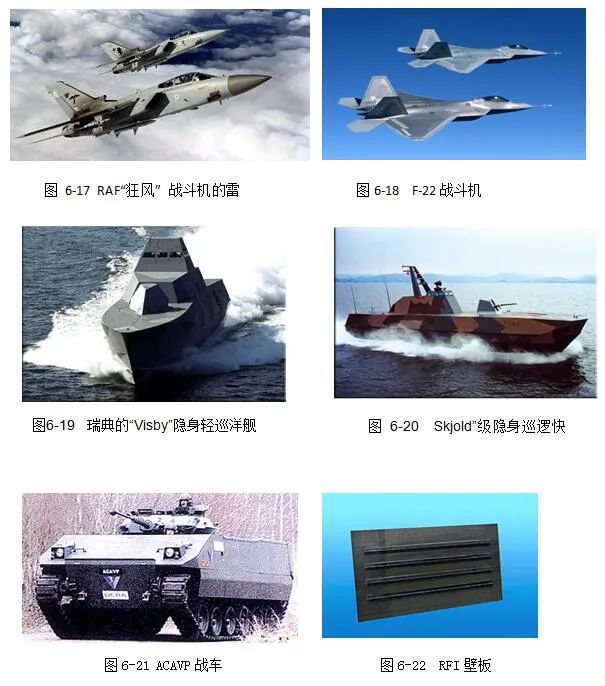
国内应用和研究RTM工艺的单位较多,如航空材料研究院、637所、703所、北京玻璃钢研究设计院、北京航空航天大学等。应用的产品有雷达罩、全碳纤维复合材料桨叶、导弹稳定翼等。 复合材料在汽车工业中的应用已经有相当长的历史,20世纪90年代以后,汽车工业开始使用RTM工艺制造零部件。汽车工业是RTM应用最早、规模最大的领域。 1970年前后,用RTM工艺加工Corvette车型的仪表盘,GM试验研究的全复合材料承力构架,达到钢制构架性能而减重20%。近年来采用RTM工艺已工业化生产了FIEERO轿车和雪佛莱LUMINA“子弹头” 汽车等车型的车身覆盖件和零部件,年产量已分别达到6.5~10万辆。1992年Chrysler研发出Viper跑车的RTM车壳;1994年Fort研发出RTM Transit商用车的高顶,1995年研制RTM Fiesta轿车的后扰流板。 Iveco卡车驾驶室的高顶采用RTM法成型,由意大利的Pianfei IPA的Mondovi厂制造。车顶总成的总面积为6m2,重量为45kg,树脂为间苯树脂,采用的预成型材料是热成型连续纤维毡。 SP5A驾驶室顶由Polymer Engineering 公司用RTM方法生产,配套服务于ERF 卡车,面积达到12m2。 材料:Class 1 BS 476 Part 7聚酯树脂; 后加工:经过计算机控制的多轴机器抛光后,进入喷涂车间。 巴西Technofibrac SA公司,广泛采用低成本的RTM成型工艺生产大型卡车车顶、面罩,豪华客车及公共汽车前脸、后尾,铺路车、油矿车车身、驾驶室总成等大型玻璃钢车辆部件,为Buscar、Ford、Volkswagen、GM、Honda等许多世界知名的汽车公司配套,1998年达到年产2,200吨的生产批量。 意大利的Sistema用RTM工艺为为Iveco车型配套制造箱式货车、卡车和教练车的车身、车顶,车顶最大达到14m2。他们认为,其优点是具有较好的空气动力学特性,在85km/h的车速下,减少空气阻力20-25%。 Advanced technology transit bus(ATTB)公司使用FRP减轻自重、减少油耗和尾气排放。由Metropolitan Transportation Authority(MTA)公司制造车体结构,比传统的公共汽车减重达4000kg,传统的公共汽车车体结构由数千个部件组成,但ATTB只有4个部件,采用VARTM复合夹芯工艺制造,选用Dow Chemical 公司Derakane环氧乙烯基树脂和PVC泡沫夹芯板,制造了包括:车顶、侧板、底盘和侧防撞板。 国内代表性的RTM工艺汽车部件有北京玻钢院生产的奥拓尾翼、半透明卡车遮阳罩、中国重汽“飞龙”卡车面罩、陕汽德御车型翼子板;北京玻璃钢制品有限公司生产的北方奔驰导流罩、二汽非金属零件公司生产的“猛士”车型的发动机罩等。
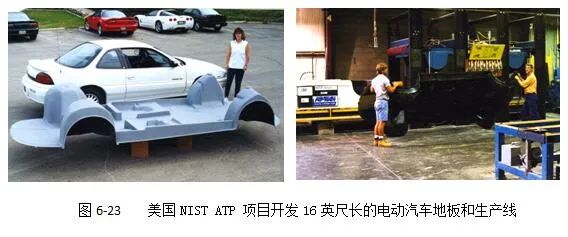
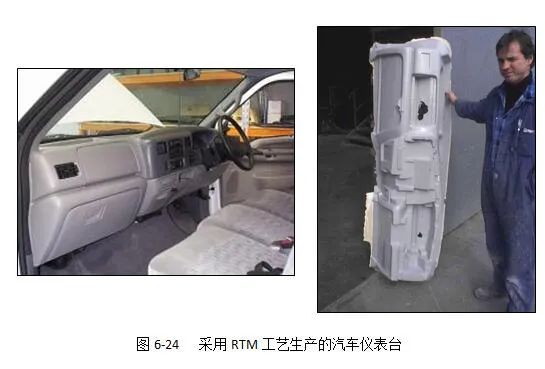
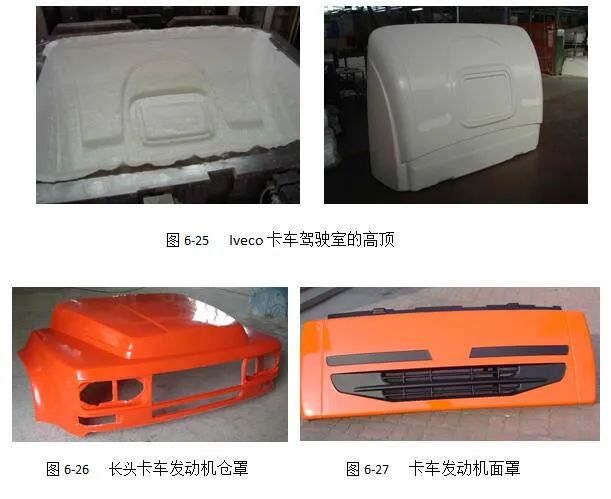
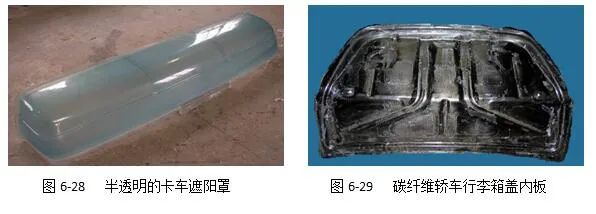
船用玻璃钢部件的特点是面积大,一般多采用VARTM技术或SCRIMP工艺制造。目前在游艇制造方面应用非常多。SCRIMP工艺特别适合制造大型复杂结构的部件,部件尺寸越大,成本优势越明显。同时,一些嵌入件,如肋、加强筋和芯材都可以在成型是放入部件中一次成型。
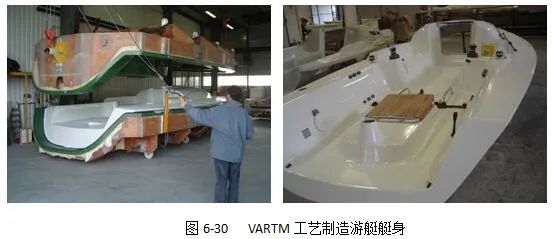
如下图所示的公用电话亭外壳,产品重量12Kg,采用Light-RTM工艺环形生产线制造。生产线单模循环周期1小时,生产线有25个模具,日产量可以达到600件。
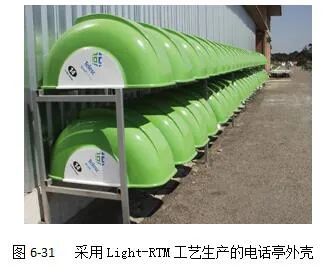
图6-32为北京玻钢院复合材料有限公司生产的RTM油站地下储油罐井盖,其特点是重量轻,承载能力高,最大可承载40吨,是比较有代表性的复杂夹芯加筋结构整体成型产品。
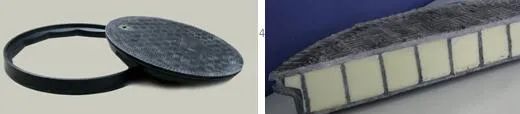
参考文献
1、黄家康 岳红军 董永褀主编.复合材料成型技术.北京:化学工业出版社.1999
2、(英)艾伦•哈珀 (中)董雨达编著.树脂传递模塑技术.哈尔滨:哈尔滨工业大学出版社.2002
3、倪爱清.复合材料液体模塑成型工艺中渗透率的研究〔D〕.武汉:武汉大学.2007
4、祝颖丹.LCM技术在线监控体系的研究〔D〕.武汉:武汉理工大学.2007
5、王庆明.RTM复合材料模具研究〔D〕.北京:北京航空航天大学.2009
文章源自:微信公众号 爱复材